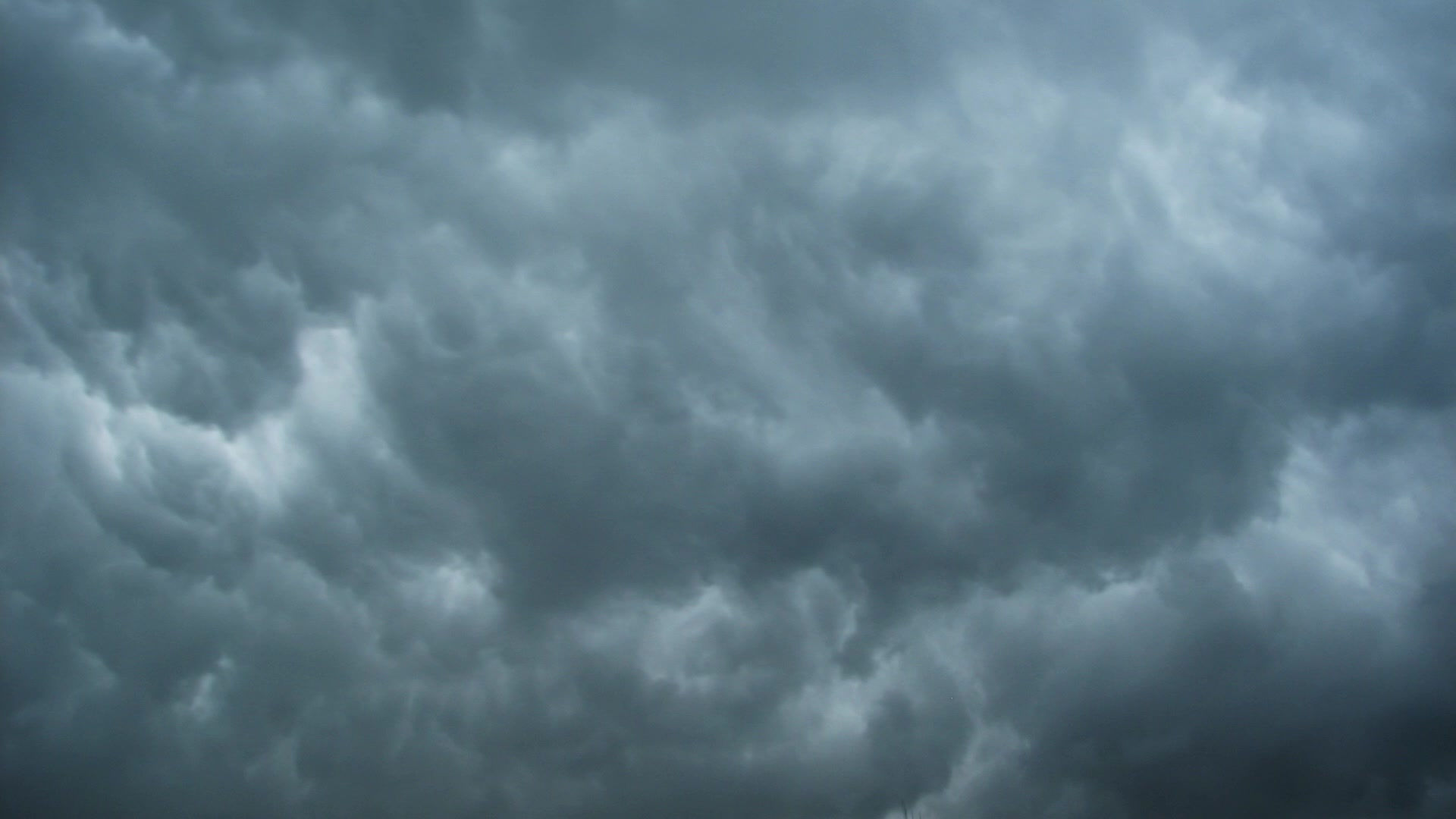
ANALYSIS
The following are details of the initial anaylisis that was done to design the Multi-Use Handtool. All calculations and Appendix referenced material can be found in the complete project report. Found under the "Project" Tab.
Impact Forces
Approach – First step is to determine the force applied on the tool during use. The tool will be used to remove soil and it is expected the soil will not be impulsive. However, it is likely the tool will come into contact with rocks and they will be. Hibbeler’s Dynamics text provides kinematic equations to help calculate the average force in a swing. In addition to the average force, the impulse exerted on the tool was calculated using the Principle of Impulse Momentum. While considering the average force on the tool the calculations for the possible deformation in the scraper tool are completed. The complete calculations are found in Appendix A.
Calculated Parameters – The calculated average force from swinging a hand tool at impact is 18 lbf (A1). This is the average force so the scraping and axe head will be designed with a safety factor of 1.5. Therefore the design force at impact is 27 lbf. The possible deformation at this force is 0.0024 in (A7.1). The calculated impulse exerted from striking an impulsive rock was 11 lbf *s (A1.1).
Stress in Tool Head
Approach – The next step is to analyze the bending stress, normal stress, and shear stress values throughout the tool head. Hibbeler’s Strengths text will provide the strategies and equations for these values. The tool will reach maximum stresses in a situation where the head is stuck or impacting a solid surface. The first stress analysis is determining the failure limits and locations if the tool head was to get stuck. These complete calculations are in Appendix A. The two tools will be welded together near the failure location of the tool analysis for the weld leg requirements were performed to ensure the weld would not be the failure (A9).
Design – The overall shape of the tool is designed to meet the minimum requirements and functions as expected. The detailed dimensions of the scraper thickness and width are adjusted to ensure the tool is not fail under normal loads and the handle will fail first. The design thickness of 3/16” for the scraping tool is based on meeting the 50 lb load design requirement (A2). In general, handles are expected to be replaced at some point before the end of the tool heads life. The greatest point of interest in the tool is where the scraper and axe head mate. This is a location with the smallest cross-sectional area and just less than the maximum moment.
Calculated Parameters – The calculated maximum load on the handle before failure is 72 lbs. at the end (A3.1). At this limit, the moment within a fixed tool head is 2524 lb*in and 1747 lb*in at the location of smallest area (A3.2). The stress at this point of interest is 100 ksi (A3.3). Using the Sy for the possible material AISI 4140 shows the handle would fail before the tool head in this situation with a safety factor of 1.6 (A3.3). The required weld leg length is .5”(A9).
Material Selection
Approach – The process of selecting a material is guided by the design requirements and the strength of the material. The design requirements demand a material that can be hardened between 50-60 HRC. This requirement is to ensure the tool will have toughness for repetitive impacts and yet be able to be sharpened. An endurance strength analysis was done to verify the material will suffice normal use. To select a material, use matweb.com and compare steel materials that have the appropriate hardenability and good for impact use.
Calculated Parameters – The material selected is AISI 4140 Steel. This is a medium –carbon steel with high hardenability and good fatigue, abrasion and impact resistance. When oil quenched, the steel has a surface hardness 57 HRC and tensile yield strength of 161 ksi (A4). The matweb.com data is in Appendix A. The calculated actual endurance strength was 33.5 ksi (A8.1). After using the “damage accumulation method” the tool will have used 50% of its life given the expected use (A-8.2).
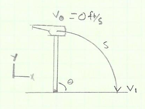

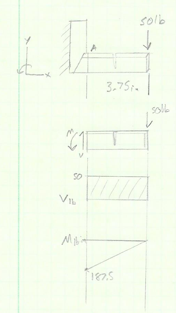
